Japan’s automated high-rise warehouses, also known as automated storage and retrieval systems (AS/RS), utilize advanced technology and equipment to achieve efficient storage and management of goods. Here are the key points of their operation:
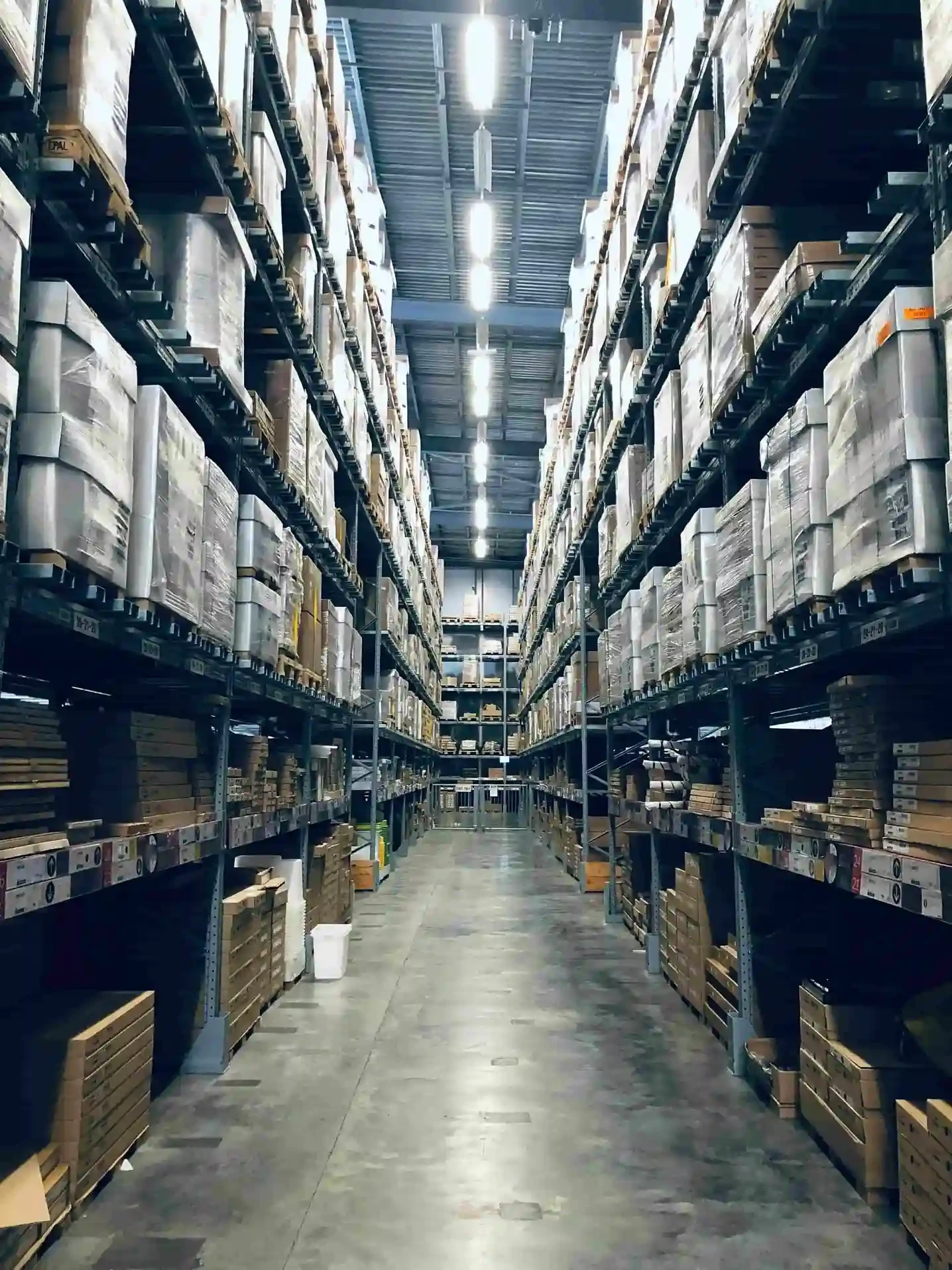
Structure and Equipment:
Automated high-rise warehouses typically consist of multi-layered racks, with heights reaching several tens of meters.
Main equipment includes stacker cranes, conveyor systems, automated guided vehicles (AGVs), robots, and sensors.
Inbound Process:
Goods are transported to the warehouse entrance via conveyor systems or AGVs.
Sensors and barcode scanning devices automatically identify the goods’ information and transmit it to the Warehouse Management System (WMS).
The stacker crane, following WMS instructions, stores the goods in designated rack positions.
Outbound Process:
When goods need to be retrieved, the WMS sends instructions to the stacker crane.
The stacker crane retrieves the specified goods from the racks and transports them to the exit via conveyor systems or AGVs.
At the exit, the goods are scanned and confirmed again to ensure accuracy.
Management and Control:
The entire warehouse is centrally managed by the WMS, which monitors the storage location and status of goods in real-time.
Through Internet of Things (IoT) technology, the equipment and systems within the warehouse can interconnect and collaborate efficiently.
Advantages:
High Space Utilization: The multi-layered rack design significantly increases the storage capacity of the warehouse.
High Efficiency: Automated equipment and systems reduce manual operations, speeding up the inbound and outbound processes.
High Accuracy: Automated identification and management systems minimize human errors, ensuring accurate storage and distribution of goods.
Japan’s automated high-rise warehouses are at the forefront globally, widely used in industries such as manufacturing, pharmaceuticals, and e-commerce. Which specific aspect of these warehouses interests you the most?